食品工場の労働環境をコンサルティングで改善!
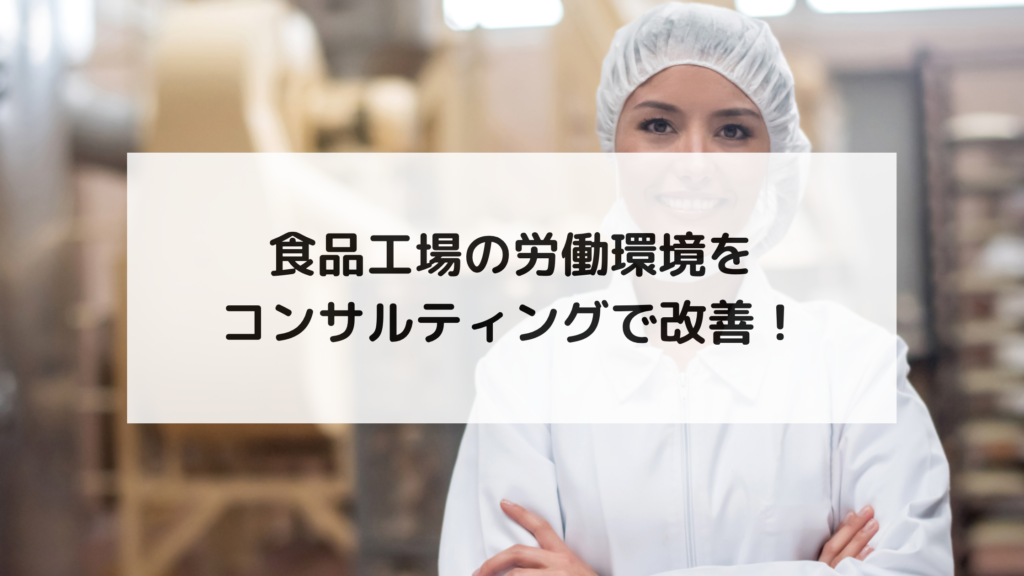
1. 食品工場の労働環境に潜む課題とは?
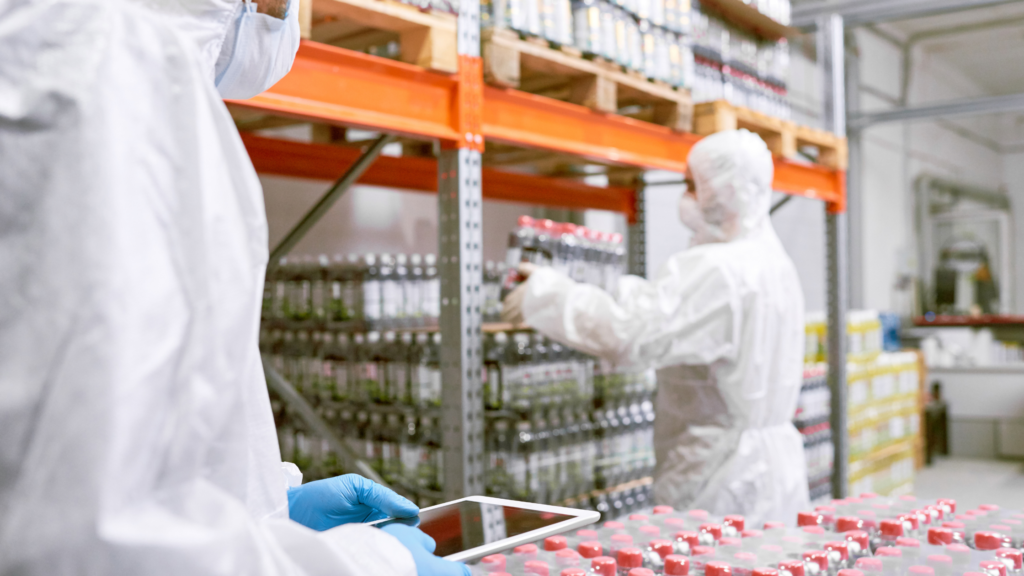
1.1 なぜ今、食品工場の労働環境改善が必要なのか
食品工場の現場は、昔から「きつい・汚い・危険」という、いわゆる3Kの代表例として語られてきました。現在でもそのイメージは根強く、人手不足や高い離職率に悩む工場が後を絶ちません。
特にここ数年で状況はさらに厳しくなっています。少子高齢化による労働力人口の減少に加えて、製造現場で働くことへの心理的なハードルも高まっています。「汚れる」「体力的にきつい」「事故が怖い」といった不安要素が、若い世代を遠ざけているのが現実です。
そんな中で、労働環境を見直すことは、単なる職場改善にとどまらず、企業の存続にも関わる重要な経営課題になっています。
たとえば、従業員の離職率が高ければ、そのたびに採用と育成に時間とコストがかかります。また、熟練スタッフが辞めてしまうことで、現場のノウハウが失われ、生産性や品質にも影響が出てしまいます。
よくある課題として、以下のようなものが挙げられます。
- 換気が不十分で夏場の作業環境が過酷
- 作業の流れが非効率で無駄な動きが多い
- 指導体制が整っておらず、新人の定着率が悪い
こうした状況を放置してしまうと、ただでさえ人材確保が難しい中で、さらに悪循環に陥ってしまいます。
また、食品を扱う工場では衛生管理の重要性も高く、働く人が安心して作業できる仕組みがなければ、安全な食品づくりも難しくなります。現場で働くスタッフの「働きやすさ」と「安心感」が、結果的に製品の品質にも直結するのです。
労働環境の改善は、従業員にとってはもちろん、企業全体にとってもプラスの効果が多くあります。このような背景から、今こそ食品工場の労働環境改善に本気で取り組む必要があると言えます。
1.2 食品工場の労働環境に多い具体的な悩みと3Kの現実
食品工場で働く現場スタッフが日々直面している悩みは、想像以上に多岐にわたります。中でも代表的なのが、「きつい・汚い・危険」という3Kと呼ばれる課題です。これらは単なるイメージではなく、現場のリアルとして今も根強く残っています。
よく聞かれる悩みには、以下のようなものがあります。
- 夏場は室温が高く、汗だくで作業するのが当たり前
- 原材料や水分が飛び散り、床が常に濡れて滑りやすい
- 重たい荷物を頻繁に運ぶため、腰や関節を痛めやすい
- 作業に追われていて、休憩が十分に取れない
こうした環境では、働く人が疲弊しやすく、体調を崩したり、最悪の場合はケガや事故につながることもあります。毎日の作業が身体的・精神的に負担となり、「長く続けられない仕事」と認識されやすくなるのが問題です。身体的・精神的に負担となり、「長く続けられない仕事」と認識されやすくなるのが問題です。
さらに、衛生面でも課題は多くあります。衛生管理の意識が低いと、床に落ちた食品の処理が遅れたり、手洗いルールが徹底されないまま作業が進んでしまうことも。その結果、異物混入や食中毒リスクといった重大な問題を引き起こす可能性もあるのです。
こうした3Kの課題をそのままにしておくと、次のような悪影響が広がります。
- 新人がすぐに辞めてしまい、採用コストだけがかさむ
- 現場スタッフのモチベーションが下がり、品質管理に支障が出る
- 消費者からの信頼を失うリスクが高まる
解決のためには、まず現場の声をしっかりと拾い上げ、何が一番ストレスになっているのかを可視化することが大事です。そして、作業の流れや設備配置、安全教育の仕組みなどを見直し、「無理なく・安全に・清潔に働ける職場づくり」を目指す必要があります。
労働環境の改善は一朝一夕ではできませんが、着実な見直しを重ねることで、スタッフが「ここで長く働きたい」と思える職場に変えていくことができます。
2. 労働環境の改善が生産性向上につながる理由
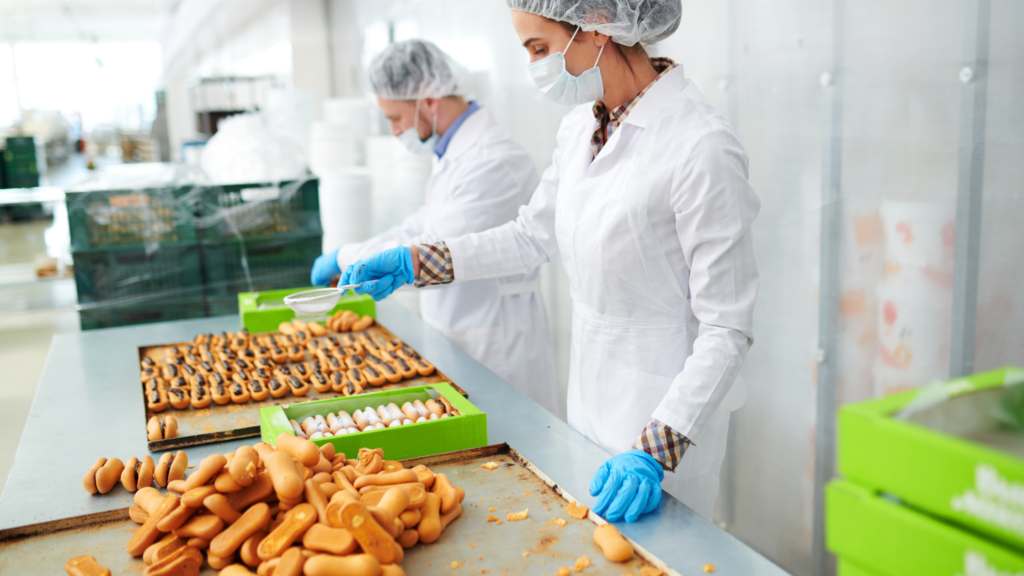
2.1 離職率・人材定着率と環境の関係性
食品工場では、「せっかく採用してもすぐ辞めてしまう」という悩みが非常に多く聞かれます。離職率の高さは、人材の確保だけでなく、教育コストや生産性にも大きな影響を及ぼします。
中でも注目したいのが、労働環境の良し悪しが離職率と直結しているという点です。
たとえば、ある調査によると、就業後3ヶ月以内に退職する理由の上位には「体力的にきつい」「職場の雰囲気が悪い」「衛生・安全面に不安がある」などが並びます。これは裏を返せば、働く環境が整っていれば、早期離職は防げるということです。
以下は、特に定着率に影響を与える代表的な要因です。
- 空調や休憩スペースが整っておらず、体力的負担が大きい
- 同僚や上司との関係性が築きにくく、孤独を感じやすい
- 衛生や安全のルールがあいまいで、不安を感じる
このような問題を放置すると、離職者が増え、人材が慢性的に不足し、既存スタッフの負担も増すという悪循環が生まれます。
逆に、働きやすい職場環境を整えることで、従業員は「ここなら安心して働ける」と感じ、定着率が大きく向上します。実際、労働環境を改善した企業では、離職率が半減し、1年以上勤務するスタッフの割合が約2倍に増えたというデータもあります。
人材の定着は、現場の安定運営に直結します。ベテランスタッフが育ち、作業効率が上がり、品質管理も安定してきます。採用コストや教育の手間も減り、長期的な人件費の最適化にもつながります。
つまり、労働環境への投資はコストではなく、「人材を育て、支えるための経営戦略」そのものなのです。
2.2 生産性を下げる現場の「ムダ」とは
食品工場の現場では、「もっと効率よくできそうなのに」と感じることが多くあります。ですが、忙しさに追われて見直す余裕がないまま、ムダな作業や非効率な動きが日常化しているケースは少なくありません。
まず、よく見られるムダな要素を整理してみましょう。
- 工程間の移動距離が長く、1日の中でかなりの時間が歩行に費やされている
- 必要な道具や資材が決まった場所に整備されておらず、探す時間が多い
- 同じ作業でも人によって手順がバラバラで、仕上がりやスピードにムラがある
- 記録や報告が紙ベースで行われており、転記ミスや時間ロスが発生している
こうした「ちょっとしたムダ」が積み重なると、1日の作業効率は大きく下がります。
たとえば、1人が1日10分ムダな動きをしていたとして、それが10人いれば100分、20日間で約33時間の損失になります。これは、ほぼ丸1人分の作業時間と同じです。
しかも、ムダが多い現場ではスタッフのストレスもたまりやすくなります。「何をどこに置いたらいいのか分からない」「人によってやり方が違うから戸惑う」といった不満が募ると、職場の雰囲気も悪くなり、離職につながるリスクも高まります。
このようなムダは、5S(整理・整頓・清掃・清潔・しつけ)や工程の見直し、標準作業の整備などによって大きく削減できます。特に外部のコンサルティングを活用すると、第三者視点から問題点を洗い出し、改善策を提案してもらえるため、スムーズな改善が可能です。
ムダを減らせば減らすほど、作業効率だけでなくスタッフの満足度も上がるというのが、現場改善の基本的な考え方です。
2.3 働きやすさが生むパフォーマンスの違い
食品工場の現場において、「働きやすさ」は決して贅沢ではなく、生産性や品質を左右する重要な要素です。作業環境が整っていれば、従業員の集中力が上がり、業務ミスや事故のリスクも下がります。
具体的には、次のような環境整備が「働きやすさ」につながります。
- 適切な空調管理で、夏も冬も快適に作業できる
- 足腰に優しいマットの設置や、重い物の持ち運びを軽減する台車の導入
- 分かりやすい作業手順書と、明確なルールの整備
- 休憩時間をきちんと確保し、リフレッシュしやすい休憩室の完備
こうした環境が整っている職場では、従業員が無理なく働けるため、集中力が持続しやすく、業務のスピードと正確性が向上します。
たとえば、空調設備がない夏場の工場では、30度を超える室温の中で作業を続けることになり、集中力が途切れやすくなります。その結果、ケアレスミスや疲労によるケガが起きやすくなり、パフォーマンスの低下を招きます。
一方、温度管理や身体的な負担を軽減する工夫があると、疲れにくくなり、作業への集中度がアップします。また、ルールが明確であれば、迷うことが少なくなり、スムーズに作業が進みます。
さらに、心理的な安心感も大事な要素です。「何かあったときに相談できる体制がある」「新人でも安心して質問できる雰囲気がある」など、メンタル面のサポートがあるだけで、離職率の低下にもつながります。
働きやすさの整備は、一人ひとりの力を最大限に引き出し、全体のパフォーマンスを底上げするカギになります。単なる福利厚生ではなく、企業の競争力を高める重要な施策として捉えることが大切です。
3. 食品工場の現場でよくある失敗と改善のヒント
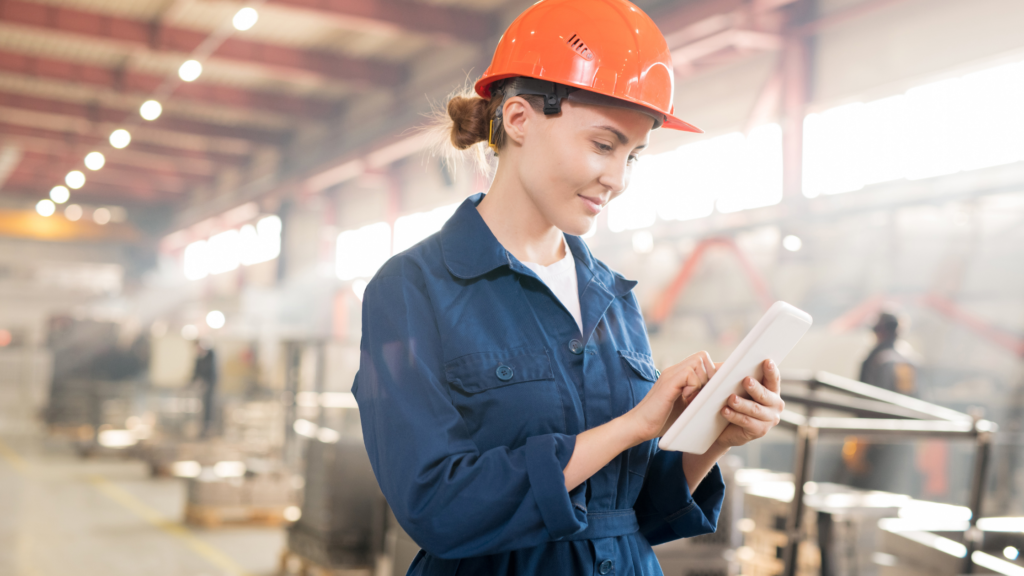
3.1 見落とされがちな安全管理の落とし穴
食品工場では衛生管理が重視されがちですが、安全管理については「当たり前だから」「今まで事故がないから」と軽視されているケースが少なくありません。しかし、実際の現場では思わぬケガや事故が起きるリスクが常に潜んでいます。
よくある安全管理の見落としポイントは次の通りです。
- 床が濡れて滑りやすい場所があるのに対策されていない
- 高所作業の安全装備が十分でない
- 動力機械の周辺で巻き込まれリスクがあるのに防護措置が不十分
- 「いつも通り」が続く中で、安全ルールが形骸化している
これらの状況を放置すると、重大な事故につながる恐れがあります。
たとえば、濡れた床に滑り止めがないことで転倒事故が起きたり、保護具の着用を怠ったことで手指の切断事故に至るケースもあります。事故が起きれば、従業員の身体的ダメージだけでなく、休職や労災申請、生産ライン停止といった深刻な影響が出てしまいます。
現場では「忙しくてつい安全確認を怠る」「ルールを守らないベテランがいる」などの声もよく聞かれます。こうした慣れや油断が、安全意識を下げる大きな原因になっているのです。
解決のためには、以下のような取り組みが効果的です。
- 危険エリアの明確化と定期的な安全点検
- ルールを守らないことへの注意喚起と指導
- 新人だけでなく全員への定期的な安全教育
- 安全装備の充実と使いやすさの改善
安全管理は「形式的にやっている」では意味がなく、現場全体の意識と仕組みが重要です。
食品工場の労働環境改善を進める上では、この安全管理の見直しが欠かせません。ケガのない安心な職場を作ることが、従業員の信頼を得る第一歩になります。
3.2 衛生管理が徹底されない理由とその対策
食品工場にとって衛生管理は命とも言える存在です。にもかかわらず、現場では「ルールはあるけれど徹底されない」「指示があっても現場で形だけになっている」といった問題がよく見られます。
衛生管理が徹底されない主な理由は以下の通りです。
- マニュアルが難解で、現場スタッフに伝わっていない
- 時間に追われ、手洗いや消毒を省略してしまう
- 「慣れ」や「いつもやってるから大丈夫」という油断
- 衛生管理が品質に直結するという意識の欠如
こうした要因が積み重なると、異物混入や食中毒などの重大な事故に繋がりかねません。
たとえば、手洗いを10秒短縮する行動が、1日何十回も繰り返されることで、大腸菌やウイルスの除去が不十分になってしまいます。また、器具の洗浄が適当になると、汚れが蓄積し、製品への影響が出るリスクも高まります。
対策として重要なのは、衛生ルールを単なる「義務」としてではなく、現場の理解と納得を得ながら徹底する仕組みを作ることです。
以下のような取り組みが効果的です。
- ポスターや動画など視覚的にわかりやすい教育ツールの導入
- ルールの背景(なぜやるのか)を説明する研修の実施
- 清掃・手洗いをチェックする仕組みの導入
- リーダーが率先して衛生行動を実践する風土づくり
また、HACCPやISO22000といった仕組みを活用すれば、衛生管理の基準が明確になり、スタッフ全員の意識が統一されやすくなります。
「ただ決める」だけでは不十分で、「現場で続けられる」工夫こそが成功の鍵です。
食品工場の労働環境改善には、衛生面の強化も不可欠。スタッフが自信を持って作業できる清潔な職場づくりが、品質の安定とクレーム削減にもつながります。
3.3 スタッフ教育が定着しない3つの原因
食品工場では、新人教育やOJTを行っていても、「教えたはずなのに守られていない」「ルールが定着しない」といった悩みがよく聞かれます。これは教育のやり方に原因がある場合が多く、放置すると現場の品質や安全性に悪影響を及ぼします。
教育が定着しない主な原因は以下の3つです。
① 教育内容が「一方通行」になっている
教える側が説明するだけで、相手の理解度を確認していないことがよくあります。用語が難しかったり、具体例がないと、聞いてもピンとこず、実際の作業に結びつかないのです。特に外国人スタッフや未経験者にとっては、専門用語の連発は大きなハードルになります。
② マニュアルが分かりにくく、使いにくい
文字だけで説明されていたり、図がなくてイメージしづらいマニュアルは、現場で読まれることがありません。たとえ一度は研修で使っても、日々の作業中に見返されることがなければ、せっかくの内容も記憶から抜けてしまいます。
③ 継続的なフォローアップがない
「研修は最初の1回だけ」「教育担当が忙しくて見てあげられない」といった状況では、身につくものも身につきません。特に慣れていない時期は、細かいサポートや声かけが非常に大事です。フィードバックがないと、間違った方法のまま作業を続けてしまう危険性もあります。
教育が定着するには、「分かりやすさ」「実践性」「継続性」の3つが欠かせません。
改善策としては、次のような取り組みが有効です。
- 写真やイラストを多用したビジュアルマニュアルの整備
- 実際の作業現場でのハンズオン形式の指導
- 教育後にミニテストやロールプレイを導入し、定着度を確認
- 月1回の振り返り面談などで習熟度をフォロー
教育は一度で終わらせるのではなく、繰り返しと見直しが前提です。「分かったつもり」を「実際にできる」に変えるには、仕組みと時間が必要です。
食品工場の労働環境を改善するには、スタッフ教育の質と継続性を高めることが、品質と安全の土台を支えるカギになります。
4. 食品工場の労働環境改善におけるコンサルティングの役割
4.1 食品工場専門のコンサルティングでできること
食品工場の労働環境を改善しようとしても、「何から手をつければいいのか分からない」「現場に慣れてしまって問題が見えにくい」といった壁に直面することがあります。そんなときに力を発揮するのが、食品工場に特化したコンサルティングの存在です。
専門コンサルタントは、現場を客観的に分析し、改善の優先順位や具体的なアプローチを提示してくれます。特に食品業界に詳しいコンサルタントは、単なる作業効率だけでなく、衛生・安全・品質までトータルで見る視点を持っています。
食品工場専門のコンサルティングでは、以下のような支援が可能です。
- 現場の動線・作業手順の分析による工程最適化
- ムダな作業や重複業務の削減による作業効率アップ
- 衛生・安全管理の体制整備(HACCP、5S、ISO対応)
- 従業員の教育プログラム作成と定着支援
- 照明・温度・湿度などの環境面からの改善提案
- 経済的負担を減らすための補助金・助成金活用サポート
現場の問題点を「見える化」し、優先度の高い部分から順に取り組むことで、無理のない改善が可能になります。
また、コンサルティングの強みは、施策を「やりっぱなし」にしないことです。定着の仕組みまで支援してもらえるため、形だけで終わる改善とは違い、実効性の高いサポートが受けられます。
工場ごとに課題や環境は異なります。だからこそ、経験豊富な第三者の視点を取り入れたコンサルティングが、より現場にフィットした改善策を生み出すのです。
4.2 現場の課題を見える化するプロセスと手法
労働環境の改善を進めるうえで大切なのが、「何が問題か」を具体的に把握することです。現場の課題は目に見えにくく、曖昧なまま対策しても効果が出ません。そこで重要になるのが「見える化」のプロセスです。
主な手法には以下があります。
- 動線調査や作業分析でムダな動きを数値化
- ヒアリングやアンケートで現場の声を収集
- 安全・衛生に関するリスクアセスメント
- 温度・湿度・照度など環境測定による体感改善
- 可視化資料の作成(現場マップ・作業フローなど)
数値や図解に落とし込むことで、現場の改善ポイントが明確になります。
4.3 改善後に得られる労働環境と業績の変化
食品工場の労働環境を整えると、スタッフの働きやすさだけでなく、企業全体に大きなメリットが広がります。改善の成果は数字や行動に現れ、持続的な成長につながります。
主な変化はこちらです。
- 離職率が下がり、人材の定着率が向上
- 作業効率アップにより生産量・納期が安定
- 不良品・トラブルが減少し品質が安定
- 安全で清潔な環境が評価され、外部監査にも対応しやすい
- 社員の満足度やモチベーションが高まり職場が活性化
労働環境の改善は、目先の対処ではなく、長期的な企業価値向上の土台になります。
5. 食品工場における労働環境改善の波及効果
5.1 働きやすさがもたらす人材定着と職場満足度
働きやすい職場環境は、人材確保や定着に直結します。「長く働ける」と感じられる環境があれば、人は自然と職場に根付き、チームの安定にもつながります。
働きやすさがもたらす効果は以下の通りです。
- 入社後の早期離職が減り、人材の育成が可能に
- 社員同士の信頼が深まり、連携が取りやすくなる
- 「ここで働きたい」という前向きな気持ちが生まれる
- 職場への愛着が高まり、自然とモラルも向上
- スタッフが安心して本来の力を発揮できる
人が辞めない職場は、それだけで強い組織になります。
5.2 生産性・品質・安全性に広がる改善効果
労働環境を改善すると、働く人の集中力や意識が変わり、現場のあらゆる面でプラスの効果が表れます。小さな取り組みでも、積み重ねることで大きな成果になります。
改善による主な効果は次の通りです。
- 作業ミスが減り、不良品や手戻りが少なくなる
- 動線や配置を見直すことで無駄が削減され生産性アップ
- 安全対策が強化され、ケガや事故のリスクが大幅減
- スタッフの集中力が持続し、作業精度が安定
- 品質に対する意識が高まり、全体のレベルが底上げされる
現場の力を最大限に引き出すには、環境づくりが欠かせません。
5.3 継続的改善で企業全体の競争力が高まる理由
労働環境の改善は、一度きりの対応では効果が薄れがちです。定期的な見直しと継続的な取り組みが、企業の競争力を長く支える力になります。
継続的改善によって得られるメリットはこちらです。
- 小さなムダや不具合に気づく体制が整う
- 問題を共有・解決する文化が根づき、職場が前向きに
- 新しい課題にも柔軟に対応できる現場力がつく
- 顧客・取引先からの信頼が高まり、商機が広がる
- 社内の意識が統一され、組織全体の動きがスムーズに
改善を続ける姿勢が、安定した品質と信頼を築くベースになります。
6. まとめ:食品工場の未来を変える第一歩を
労働環境の改善というと「大がかりな設備投資が必要」と思われがちですが、実は日々の小さな見直しの積み重ねこそが、大きな成果を生み出します。
小さな改善が効果を生む理由はこちらです。
- 現場の不満や不便を解消することで作業効率がアップ
- 負担軽減により、ミスや事故のリスクが減少
- 少額でできるため、すぐに取りかかれる
- 現場の声を反映しやすく、スタッフの納得感も高い
- 成功体験の積み重ねが、さらに改善意欲を引き出す
改善は「一歩ずつ続ける」ことが最大の成果を生みます。
食品工場の労働環境改善ならTMTユニバーサル株式会社にお任せください。
工程のムダ削減や衛生・安全対策、スタッフ教育まで、現場の課題に合わせた最適な改善策をご提案します。
労働環境のトータルサポートをお探しなら、TMTユニバーサル株式会社のサービス内容をご確認ください。
- 関連タグ
- 労働環境