食品工場の生産性向上はプロのコンサルティングで変わる
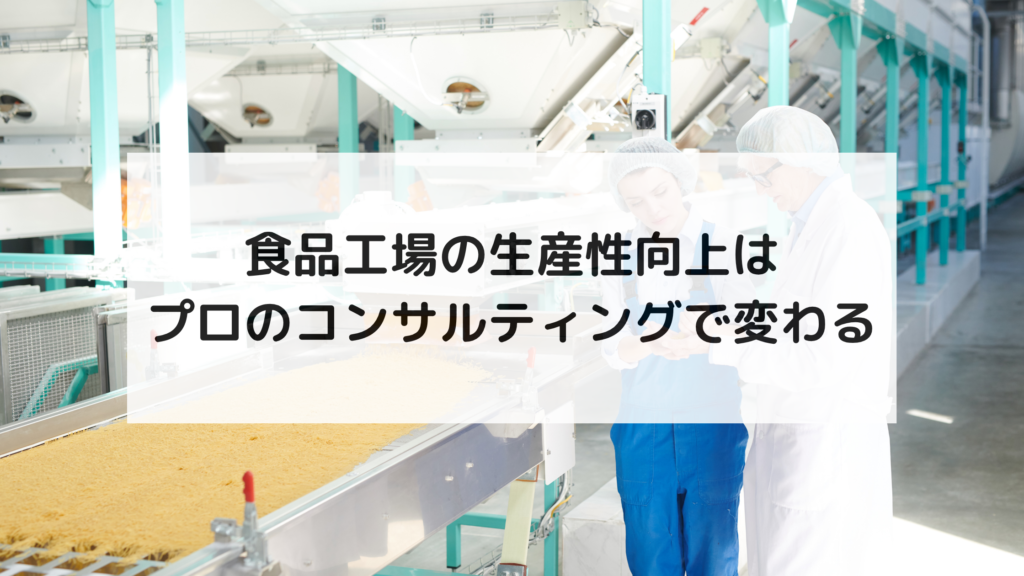
1. 食品工場の生産性向上にコンサルティングが必要な理由
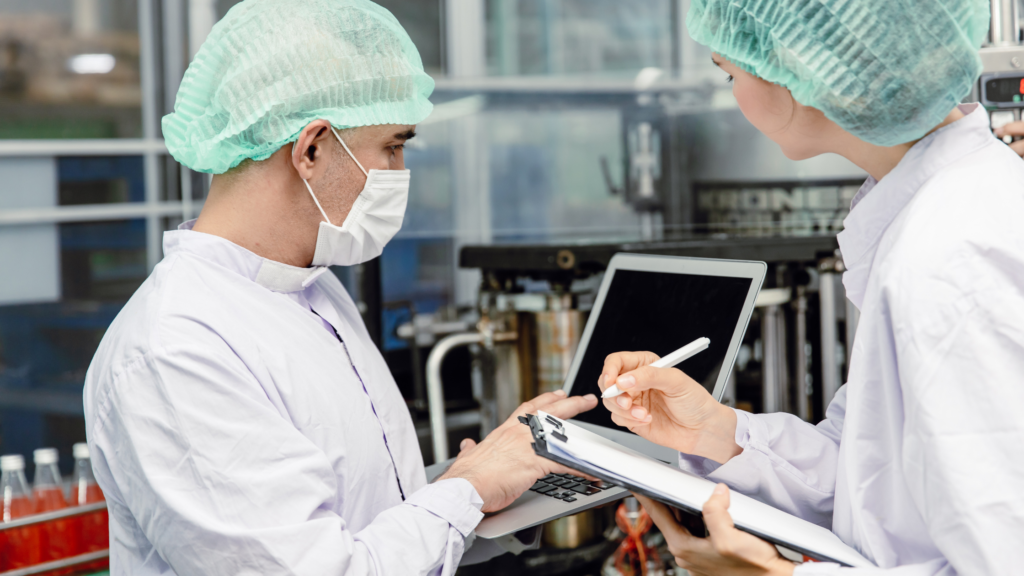
1.1 食品工場における生産性の課題とは
食品工場では、日々多くの人と機械が動き続けています。
一見スムーズに見えても、よく見ると「ムダ」が潜んでいることが多いです。
生産性を上げるためには、まずその課題を把握することが大事です。
よくある課題は、大きく次の3つに分けられます。
- 作業の非効率さ
- 同じ工程を複数の人が二重に行っている
- 部品や原料の配置が悪く、無駄な移動が多い
- 生産スケジュールが属人的で、手待ち時間が発生
- 同じ工程を複数の人が二重に行っている
- 人手不足と高い離職率
- 慢性的な人手不足で、一人あたりの負担が増大
- 定着率が低く、常に新人の教育に追われる
- 繁忙期に対応できる人員確保が難しい
- 慢性的な人手不足で、一人あたりの負担が増大
- 品質・衛生管理の課題
- HACCPなどの基準に沿った管理が形骸化している
- クレームが発生しやすい工程が放置されがち
- マニュアルがあっても現場に浸透していない
- HACCPなどの基準に沿った管理が形骸化している
こうした課題を放置すると、工場全体の生産性が大幅に下がるだけでなく、品質事故や人材流出といった深刻な問題にもつながります。
たとえば、無駄な作業を削減するだけで「1日あたりの稼働時間を1時間短縮」できたケースも珍しくありません。
さらに人員配置や工程設計を見直せば、同じ人数で「生産量が1.5倍」になることもあります。
忙しい毎日で現場を見直す時間がないまま、非効率なやり方が習慣化してしまう…。
そんな悩みを抱えている食品工場は少なくありません。
だからこそ、現場を客観的に分析できる第三者の視点=コンサルティングが必要になるんです。
1.2 コンサルティング導入のメリット
食品工場の課題を解決するには、自社だけの力では限界があります。
そんなとき頼れるのが、専門家によるコンサルティングです。
生産性向上に特化したコンサルティングには、次のようなメリットがあります。
客観的な視点で現場を診断してくれる
内部の人間では見逃しがちな「ムダ」や「非効率」に気づいてくれるのが大きな強み。
第三者が入ることで、感情に左右されず冷静な判断が可能です。
たとえば、次のような指摘がよくあります。
- 原料の置き場所が遠くて移動時間が無駄にかかっている
- 作業員の配置が偏っており、一部のラインだけが混雑している
- 曖昧なマニュアルが原因で作業ミスが多発している
これらは現場で働いていると見えづらくなってしまう点。
コンサルタントがいることで、見直しのきっかけが得られます。
数値と実績に基づく改善提案
単なるアドバイスではなく、「何を、どう改善すれば、どれだけ効果が出るのか」を具体的な数値で示してくれます。
たとえば、
- 稼働率が60%から85%に改善
- 不良品率が2.5%から1.0%に削減
- 作業時間が1日あたり2時間短縮
といった、目に見える成果が期待できるんです。
教育・人材育成にもつながる
コンサルティングの一環として、作業員向けの研修や指導を行ってくれる場合もあります。
現場に必要なスキルが根付くことで、教育時間の短縮や離職率の低下にもつながります。
「現場が変わると、働き方も変わる」
これが、コンサルティングの一番の価値かもしれません。
プロの手を借りることで、工場の雰囲気そのものが前向きに変化していきます。
2. 生産性向上を阻む3つの落とし穴と改善アプローチ
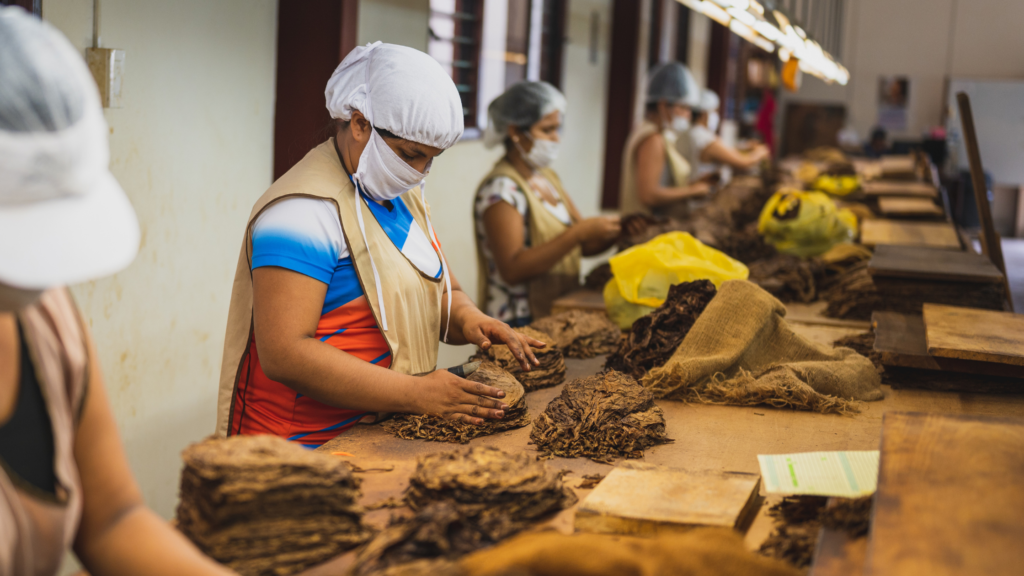
2.1 無駄な作業動線とレイアウトの非効率化
食品工場の現場では、作業の動線やレイアウトが生産性を大きく左右します。
動線が悪いと、移動距離や作業時間が増えるだけでなく、作業者の疲労やストレスも蓄積していきます。
よくある失敗例とその影響
こんな動線ミス、思い当たることありませんか?
- 原料の保管場所が遠すぎて、何度も往復する
- 加工から包装までの導線がジグザグで、カートが通りにくい
- 出荷口が搬入口と重なり、作業が頻繁に中断される
これらの状態が続くと、1日あたり30〜60分の作業ロスが発生してしまうことも。
結果的に、残業が常態化し、作業効率も落ちてしまいます。
生産性向上のための動線改善ポイント
生産性をアップさせるには、以下のような点を見直すことが重要です。
- 加工・包装・検品・出荷の順番に沿った直線的な動線設計
- 使用頻度の高い道具や資材は、すぐに手が届く場所へ配置
- 台車やフォークリフトの通行経路を確保し、スムーズな搬送を実現
実際、動線を見直しただけで作業時間が20%短縮できたという結果もあります。
忙しい中でも、少しの見直しで大きな効果が出るのが動線改善のメリットです。
レイアウト設計はプロの視点で最適化
食品工場のレイアウト設計には、衛生管理やHACCPへの対応も欠かせません。
ゾーニングが曖昧だと、交差汚染や異物混入のリスクが高まります。
コンサルティングでは、こうした衛生面も考慮して、作業の流れに合った効率的かつ安全なレイアウトを提案してくれます。
作業動線とレイアウトを見直すことで、驚くほどスムーズに現場が回り始めるんです。
2.2 作業員のスキルばらつきと教育不足
食品工場では、作業員のスキルが安定していないと、生産ライン全体の効率が下がることが多いです。
経験者と新人で作業スピードや精度に差があると、ミスやトラブルが起きやすくなります。
よくある問題と現場の混乱
以下のような状況は、多くの工場で見られます。
- マニュアルが曖昧で、やり方が人によって違う
- ベテランが属人的に作業を抱えてしまい、他の人が対応できない
- 新人が育たず、戦力になるまでに時間がかかる
このような状態だと、「誰が休んでも同じ品質が保てる」体制が作れません。
結果的に、ムラのある生産になってしまい、不良品率が上昇したり、ライン停止につながったりします。
教育体制を整える3つのポイント
作業員のスキルを底上げするには、以下のような教育体制の整備が欠かせません。
- 標準作業手順書(SOP)の明確化と浸透
写真付きや動画付きで直感的に理解できるマニュアルを整備 - OJTとOFF-JTの使い分け
実作業と座学を組み合わせて、知識と実践の両面をカバー - スキルマップの導入
各作業員がどの業務をどれだけこなせるかを見える化し、教育の優先度を明確に
これにより、現場の「属人化」を防ぎ、誰でも同じレベルで作業できるようになります。
コンサルティングによる研修設計
コンサルタントの支援では、現場に即した教育プランの設計や研修の実施まで対応してくれるケースがあります。
単なる座学ではなく、現場目線で必要な知識・技能を教えるのが特徴です。
スキルが平準化されると、作業のバラつきがなくなり、ライン全体が安定して動くようになります。
2.3 機械トラブルや設備老朽化の見落とし
食品工場の生産性に大きく影響するのが、機械や設備の不具合です。
「いつも通り動いているから大丈夫」と思っていたら、急なトラブルでラインが止まる。
そんな事態は少なくありません。
見落とされやすいトラブルの兆候
現場では、次のような初期症状を見逃してしまうことがよくあります。
- 機械の異音や振動が以前より大きい
- 包装機のずれやラベルの印刷ミスが頻発
- 一部のパーツだけ修理を繰り返している
こうした不調が放置されると、ある日突然大きな故障につながり、数時間〜1日単位のライン停止に発展することも。
突発的なトラブルで1日ラインが止まると、売上損失は数十万円に及ぶケースもあります。
設備の保守・点検を仕組み化することが大事
生産性を落とさないためには、機械や設備の状態を「勘」ではなく「ルール」で管理することが必要です。
- 定期的な点検チェックリストの運用
- 稼働時間や使用頻度に基づく部品交換サイクルの設定
- 簡単なメンテナンス作業の社内教育
これらを習慣化することで、トラブルの予防につながります。
コンサルティングの視点で予防保全を強化
生産性向上のコンサルティングでは、現場の保守体制を見直すサポートも行います。
設備の稼働ログを分析したり、故障履歴をもとに予防保全計画を立てるなど、専門的な手法で改善を進めていきます。
トラブルを「起きてから直す」から「起きる前に防ぐ」へと考え方を変えるだけで、生産性は大きく変わってきます。
3. 食品工場でのコンサルティングの具体的な支援内容
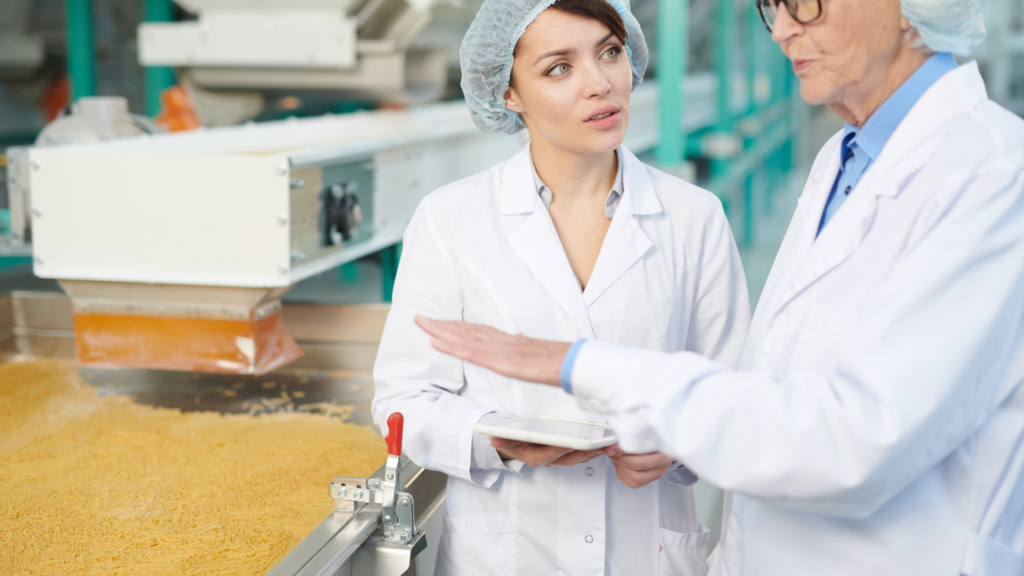
3.1 生産工程の見直しと稼働率の最適化
食品工場の生産性を高めるうえで欠かせないのが、生産工程の最適化です。
どれだけ人材や設備が整っていても、工程の流れが悪ければ、作業効率は上がりません。
稼働率が下がる原因は「ムダな待ち時間」
以下のような原因が、稼働率を下げてしまうことがあります。
- 原料が届かず、作業が始められない
- 機械の立ち上げに時間がかかり、稼働が遅れる
- 検品や包装の工程でボトルネックが発生
これらはすべて、「段取りのズレ」や「工程間の不均衡」が引き起こしています。
実際、こうした待ち時間が1日あたり1〜2時間にもなることがあります。
工程見直しのための3つのステップ
生産工程の改善は、以下のステップで進めると効果的です。
- 現状の工程フローを可視化する
時系列で工程ごとの作業時間・人員配置・停止要因を洗い出す - 非効率なポイントを特定する
待ち時間が多い工程、ミスが頻発する部分、過剰品質の見直しなど - ボトルネックを中心に再設計する
全体のバランスを見ながら、スムーズに流れるように再構築
この見直しによって、稼働率が70%から90%に上昇したという成果も得られています。
コンサルティングによる工程分析の強み
専門家が介入することで、現場の感覚に頼らず、データに基づく改善が可能になります。
タクトタイム(作業時間の基準)や稼働ログなどを分析して、最も効果のある改善策を提案してくれます。
「どこを変えれば、どれだけ良くなるのか」が見えることで、現場の納得感も高まります。
特に食品工場では、製造・検品・包装と多工程にわたるため、工程全体のバランスを取ることが重要です。
一部の工程だけを改善しても、他が追いつかず結局ムダが発生してしまいます。
その点、コンサルティングでは工場全体を俯瞰して、最適な流れを作るための戦略的な提案を行ってくれます。
工程の再設計は、生産性向上のカギを握る重要なステップです。
3.2 人材採用・育成サポートによる労働力の安定化
食品工場の生産性向上には、安定した人材の確保と育成が不可欠です。
人が定着し、スムーズに働ける体制が整っていないと、どれだけ設備や工程を改善しても、成果は限定的になります。
人手不足と定着率低下の背景
現在、多くの食品工場が抱えているのが次のような悩みです。
- 求人を出しても応募が集まらない
- 採用しても数ヶ月で退職してしまう
- 教育に時間がかかり、現場が回らない
とくに繁忙期には、人員の確保が生産の成否を左右する要因になります。
採用がうまくいかないことで、既存スタッフの負担が増え、さらに離職が加速するという悪循環も。
採用から定着まで一貫サポートするメリット
コンサルティングの支援では、単なる採用活動だけでなく、「人が育つ環境づくり」までをトータルでサポートしてくれます。
以下のような支援内容が含まれます。
- 現場に合った求人票・媒体の選定と戦略的な採用計画
- 面接・採用フローの改善によるマッチング精度の向上
- 入社後のフォロー体制構築と教育カリキュラムの整備
こうした支援を受けることで、採用から現場定着までの時間が約30%短縮されるケースもあります。
教育体制の強化でスキルの底上げを実現
さらに、採用した人材が戦力化するには、教育と育成の仕組みが欠かせません。
- 新人向けのステップ別研修プログラム
- 現場リーダー層へのマネジメント研修
- 外国人労働者向けの多言語対応マニュアル作成
このような取り組みを行うことで、離職率を50%以下に抑えることも可能になります。
人材が安定して初めて、設備や工程改善の効果が最大限に発揮されます。
3.3 職場環境改善で定着率アップと安全性向上
食品工場の生産性向上において、職場環境の整備は見逃せない要素です。
快適で安全な環境が整っていないと、スタッフは長く働けず、モチベーションも低下してしまいます。
よくある職場環境の課題
以下のような点が、現場の生産性に影響を与える要因になります。
- 空調が不十分で、夏は暑く冬は寒い
- 床が滑りやすく、転倒事故が多い
- 騒音・振動が強く、集中しにくい
また、作業スペースが狭く、身体的な負担が大きいと、従業員の健康にも悪影響が出てきます。
これらの環境的ストレスが、離職や作業ミスの原因になってしまうこともあります。
安全性と快適性を両立するポイント
生産性を高めるためには、次のような取り組みが効果的です。
- 照明・空調・換気の最適化
視認性を高め、疲労軽減や集中力向上につながる - 床材や作業靴の見直し
転倒事故を防ぎ、安全意識を高める - 休憩スペースやロッカールームの整備
精神的なリフレッシュができる環境を整える
こうした施策によって、作業効率が10〜20%向上するケースも見られます。
コンサルティングで整える「働きやすさ」
食品工場に特化したコンサルティングでは、「安全性」「衛生面」「作業快適性」のバランスを考慮した職場環境づくりを提案してくれます。
たとえば、
- 騒音軽減のためのパネル導入
- 動線改善に伴う事故リスクの低減
- メンタルヘルス支援体制の導入
といった多面的なサポートが可能です。
働きやすい環境が整うと、自然と定着率が上がり、現場に活気が戻ってきます。
4. 数値で見る生産性向上の成果と変化
4.1 作業時間短縮・人員削減などの定量的成果
食品工場の生産性向上は、数値での改善効果がはっきり出やすいのが特徴です。
コンサルティング導入により、以下のような成果が得られます。
- 作業工程の見直しにより、1日の作業時間を最大2時間短縮
- ラインの人員再配置により、必要人員数を15〜20%削減
- 動線・レイアウト改善で、製造効率が約30%向上
改善前後で定量的な比較を行うことで、投資対効果(ROI)の算出も可能になります。
これにより経営判断がしやすくなり、改善の継続もしやすくなります。
数字で成果が見えると、現場の納得感も高まり、改善が定着しやすくなります。
4.2 衛生・品質管理の強化によるクレーム減少
食品工場では、衛生・品質管理の徹底が信頼維持に直結します。
コンサルティングを通じて、次のような改善が期待できます。
- HACCP対応のマニュアル整備で、チェック漏れを大幅に削減
- 品質検査の基準見直しにより、不良品率を2.5%→1.0%へ改善
- クレーム原因の工程分析で、月間クレーム件数が半減
作業員の衛生意識も向上し、現場の緊張感と品質意識が安定化します。
結果として、ブランドイメージや顧客満足度の向上にもつながります。
衛生・品質管理を見直すことで、トラブルの“予防”が実現します。
4.3 現場の士気向上と離職率の改善
生産性向上の成果は、作業環境の改善を通じて現場のモチベーションにも波及します。
働きやすさが向上すれば、自然と定着率も高まります。
- 明確な評価制度の導入で、頑張りが可視化され士気アップ
- 作業負担の平準化により、ストレスや不満が減少
- 教育・研修制度の整備で、新人の早期戦力化と安心感を提供
これにより、離職率が30〜50%改善された事例もあります。
人が安定することで、長期的な現場力の向上に直結します。
「辞めない現場」をつくることが、持続的な生産性向上の基盤になります。
5. コンサルティング導入のステップと成功のコツ
5.1 現状分析から課題抽出までのプロセス
生産性向上の第一歩は、現状を正しく把握することです。
コンサルティングでは、客観的な視点で課題を浮き彫りにしていきます。
- 現場ヒアリングと観察により、実際の作業フローを可視化
- 稼働率・歩留まり・人員配置などの定量データを分析
- 問題点を「工程・人材・設備・管理」に分類して整理
このプロセスにより、感覚ではなく事実に基づいた改善案の立案が可能になります。
また、従業員の意見を取り入れることで、現場の納得感も高まります。
的確な現状分析が、改善の成否を左右する鍵です。
5.2 改善施策の実施とフォローアップ
課題が明確になったら、次は実際の改善行動に移すフェーズです。
コンサルティングでは、現場に合った施策を具体的に実施していきます。
- 作業マニュアルやレイアウトの見直しなど、即効性のある施策を優先実行
- 進捗状況を定期的に確認し、柔軟に改善方針を修正
- 教育・研修・面談を通じて、スタッフの理解と協力を促進
さらに、導入後の変化を定量的に評価(作業時間・稼働率など)することで、成果を見える化できます。
フォロー体制があることで、改善が一過性で終わらず、定着します。
5.3 成功事例に学ぶ導入のポイント
成功している食品工場には、共通する導入のコツがあります。
コンサルティングをうまく活用するには、以下の点が重要です。
- 現場全体で目的を共有し、「なぜ変えるのか」を明確化
- 小さな成功体験を積み重ね、段階的に成果を広げる
- 改善結果を見える化し、スタッフのモチベーションを維持
また、現場リーダーの巻き込みが早いほど、現場の動きがスムーズになります。
改善が進むことで現場の空気が変わり、「やれば変わる」という実感が広がっていきます。
成功のカギは、現場との信頼関係と小さな前進の積み重ねにあります。
6. まとめ
6.1 今こそ始めたい生産性向上の取り組み
人手不足やコスト上昇が続く中で、食品工場の生産性向上は急務となっています。
今取り組むことで、将来的な競争力に大きな差が生まれます。
- 現場の改善余地を洗い出すことで、無理なく効率アップ
- 人材の定着や育成を進め、安定した稼働体制を確保
- 品質や安全性の強化で、クレーム削減と信頼向上
外部の専門家の視点を取り入れることで、これまで見逃していた改善点が見えてくることもあります。
早めの一歩が、未来の工場の安定と成長につながります。
6.2 プロのコンサルティングで変化を実感しよう
自社だけで生産性を改善しようとしても、気づかない課題が多く残るものです。
だからこそ、プロのコンサルティングが頼りになります。
- 専門家の客観的な分析で、改善ポイントが明確に
- 数値と実例に基づく提案で、納得感と再現性が高い
- 継続的なフォローで、現場に改善が定着しやすい
改善の成果が見え始めると、現場の空気が変わり、従業員の意識も前向きになります。
この変化こそが、コンサルティングの最大の価値です。
プロと一緒に進めることで、成果を“実感”できる改善が実現します。
食品工場の生産性を本気で変えたいなら、TMTユニバーサル株式会社へ
TMTユニバーサル株式会社では食品工場に特化した支援を展開中。経験豊富なコンサルタントが現場の声に寄り添い、確かな成果を導きます。
ムダの削減・人材の定着・品質向上までサポート可能です。
詳細は公式サイトをご覧ください。
- 関連タグ
- 生産性向上